Designing, building, and operating a constellation of Synthetic Aperture Radar (SAR) satellites is no small task and requires a ton of hard work from a long list of teams across the entire company. The spacecraft integration and test team is one link in the chain with the objective of producing flight worthy spacecraft to meet our launch schedule and is the last stop for our spacecraft before joining our constellation. Working on the highest assembly level in a manufacturing environment, our team is in a unique position to collaborate with brilliant engineers from every corner of the company to resolve technical issues as they arise to guarantee that our spacecraft are ready to contribute to the greater goals of our constellation.
Functional Testing: Design to Execution
One of the responsibilities of our team is to subject the spacecraft to functional testing to ensure that every component is operating as intended on the ground. Our team both designs and executes these tests, which is a big task for a small team, so automation is at the core of our testing philosophy which allows us to not only be time efficient but allows for repeatable testing and enables better test analytics.
After the test has been built, reviewed, and released, our team will execute the testing on the vehicle over many key milestones of theI&T campaign. Working closely with our mechanical team, a sequence of functional test and build steps are performed to go from an assortment of components to a fully assembled spacecraft ready to do battle with the harsh environments of launch and space.
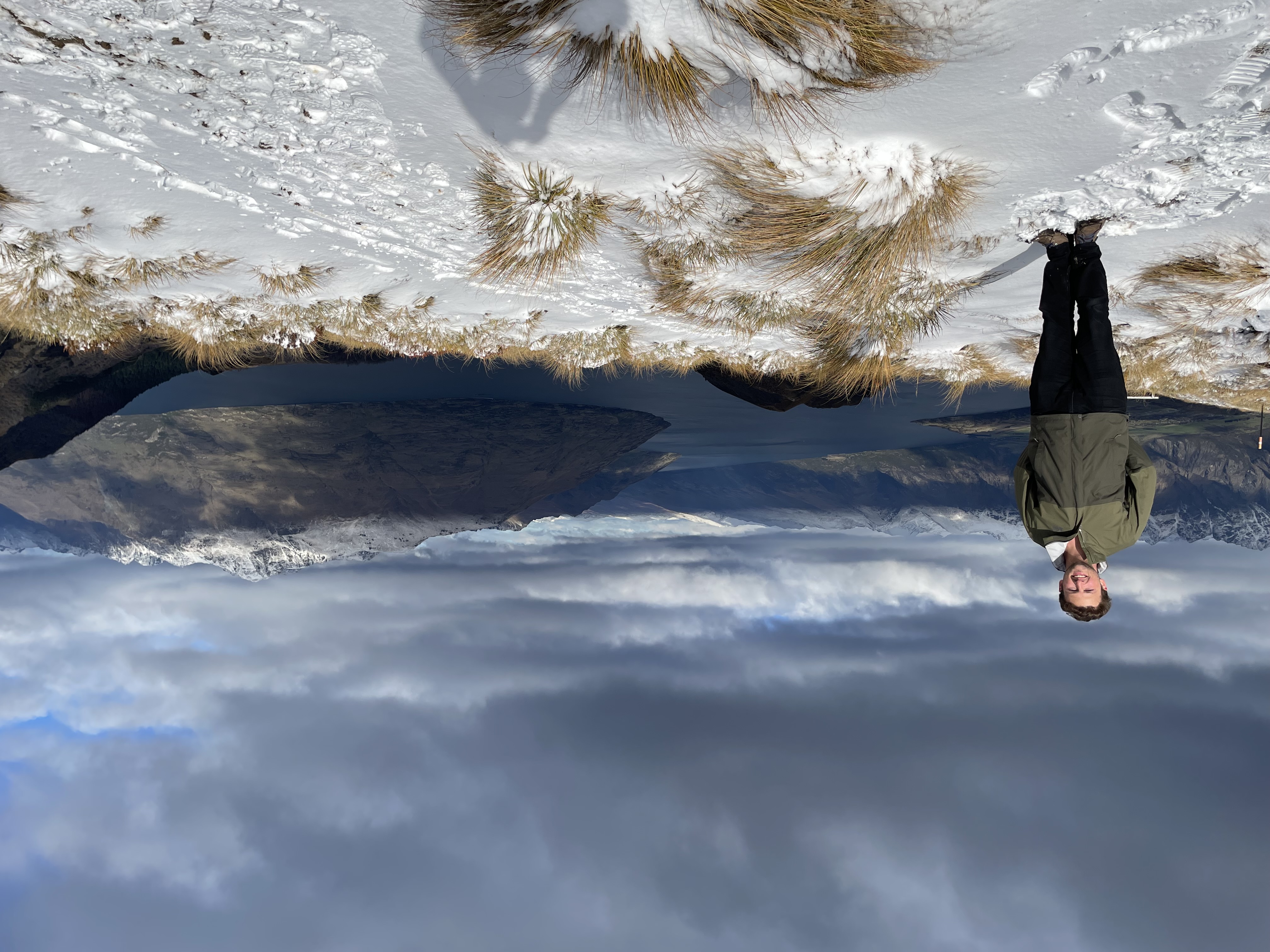
Environmental Testing: Shake and Bake
With the spacecraft built up, we need to prove that the vehicle can survive the flight and operating environments that it will see through launch and its mission lifetime. First step in this process is vibration testing where we mount the vehicle on a shaker table, instrument it with accelerometers in critical locations, and recreate the launch environment to verify that the dynamic loads from the launch vehicle will not excite any dangerous responses in our spacecraft, protecting both our hardware and others flying on the same mission.
Once we have endured the launch environment, we need to confirm that the vehicle can survive the harsh thermal environment that it will see for the remainder of its mission. Our team sets up the vehicle in our thermal vacuum chamber and once pumped down to a hard vacuum, we cycle the vehicle between hot and cold cycles running functional tests at each plateau to verify our hardware operates nominally at the expected thermal extremes. This is one of the higher risk tests that we run on spacecraft in test, requiring 24/7 shift operations by the team supported by a highly automated system that monitors and alerts on telemetry coming from the spacecraft, chamber, and ground support equipment to safely accomplish the test.
Deployables Testing: Zero G Testing
After being exposed to environmental testing, we want to confirm that our deployable structures still deploy nominally once reaching orbit. Working with our deployables team, we setup the boom, and reflector antenna on Zero-G off-loaders to mimic microgravity environments and command the spacecraft the same way we will during commissioning to confirm that these dynamic structures still deploy correctly after being exposed to environmental testing.
Flight Integration: End of the Road
Once the deployable structures have been reinstalled for flight, my team will install the separation system, which rigidly mounts our spacecraft to the launch vehicle and maintains the spacecraft in a powered off state until actuated where it separates the spacecraft from the launch vehicle and enables the flight computer to boot up to begin its life on orbit. Working with our mission director and the launch service provider, the mission specific hardware that mates the spacecraft to launch vehicle is identified and installed, as well as determining/assembling the support equipment we will need to hoist the spacecraft onto the launch stack for the final mate to the launch vehicle.
Once all hardware is integrated to the spacecraft, and lifting GSE is built, it’s time for the final journey to the launch site. Depending on the mission, our team is sent to various launch sites around the world to perform the final operations on the vehicle before launch. After arriving at the launch site, the vehicle is inspected and ran through one last functional test to verify all systems are healthy before arming the vehicle for flight so that the next time the spacecraft boots up in space, it will autonomously step through the solar array deployments and power generation sequence before waiting for input from one of our satellite operators. Once armed and powered down, the vehicle is ready to be integrated for flight and the team hoists the spacecraft onto the launch vehicle finishing the ground processing of a Capella spacecraft set to join the constellation.
The Pay Off
Working on Capella’s spacecraft and with this team has been one of the most rewarding experiences of my life, learning more and more everyday, surrounded by curious innovators working at the forefront of space technology. At the same time, the team and our mission are challenging me everyday to be a better engineer and a better manager, which pays itself back to the team by creating that same rewarding environment that I think attracts a lot of talented folks to Capella, enabling us to progress rapidly towards the goals we set as a company.